Год назад в России стартовал национальный проект «Производительность труда и поддержка занятости», нацеленный на улучшение качества жизни и труда работающих граждан. Добиться такого результата возможно, если сотрудники компаний будут работать эффективнее, считают эксперты. Нацпроект в части адресной поддержки предприятий реализует Федеральный центр компетенций в сфере производительности труда (ФЦК), сотрудники которого во главе с генеральным директором Николаем Соломоном внедряют на предприятиях инструменты бережливого производства, позволяющие им улучшать не только операционные показатели, но и экономические. Как это происходит на практике — в материале «Ленты.ру».
Без разрухи в головах
Существует распространенный стереотип: в новых производственных технологиях нуждаются лишь компании, зародившиеся еще в Советском Союзе. В более молодых организациях, начавших свое становление вместе с возрождением рыночной экономики в России, такой проблемы нет. Однако будь это так, Россия давно бы уже могла похвастаться своими собственными Apple, Tesla или Toyota. В модернизации могут нуждаться все, вне зависимости от того, сколько лет компания существует на рынке, и даже от того, насколько развита ее производственная система.
В декабре 2018 года ФЦК начал работать с участником нацпроекта — молодой, инновационной компанией из Татарстана «Эйдос-Медицина», занимающейся разработкой и производством медицинских симуляторов. Эти устройства позволяют студентам и врачам повышать квалификацию, отрабатывая операции на них, а не на живых людях.
С компанией работали два эксперта ФЦК и три специалиста Регионального центра компетенций Татарстана — такие организации специально создаются в регионах, потому как количество предприятий, присоединяющихся к нацпроекту, постоянно растет: сейчас их уже более 1100. Для оптимизации производственных потоков на «Эйдос-Медицине» был сформирован проектный офис, сотрудники которого прошли обучение инструментам бережливого производства, чтобы внедрить их на пилотном потоке. В качестве такого потока решили выбрать производство хирургических тренажеров. Эксперты провели диагностику: визуализировали, как проходит производственный процесс, как перемещаются операторы, насколько логично расположено оборудование, есть ли простои.
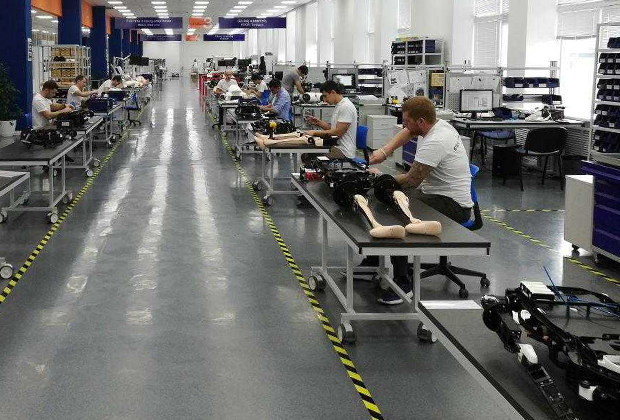
Фото: ФЦК
Основная проблема потока — предприятие производило сразу большие партии продукции, из-за чего весь процесс ее изготовления шел медленно. Когда один оператор, выполняя работу оперативнее, освобождался, другой еще заканчивал работу. Тогда первому приходилось ожидать своей очереди, при этом на его рабочем месте скапливались запасы, что мешало работать. С подачи специалистов ФЦК было принято решение производить продукт поштучно: теперь каждая заготовка передавалась на следующую операцию сразу, конечный продукт производился быстрее. Это позволило сократить время, затрачиваемое на производственный цикл, на 40 процентов.
«Мы стихийно развиваемся, и каждый год нам требуется все больше ресурсов для производства», — рассказывает ведущий инженер-технолог компании Рамиль Яруллин, прошедший обучение по программе «Лидеры производительности». «Собственно, все линейные руководители нашей компании выросли из рядовых сотрудников, и это, конечно, большой плюс со многих точек зрения. Но профессиональных навыков, прямо скажем, не хватало», — посетовал он. При этом Яруллин отметил, что «Федеральный центр компетенций дает академичный подход к производству, который позволяет находить на своем участке какие-либо потери и их устранять. А только найти первопричину проблемы на самом деле сложно».
В качестве примера ведущий инженер-технолог компании увлеченно рассказывал об инструменте диаграмма «спагетти», с помощью которого можно на бумаге нарисовать и производственную площадку, и движение материальных потоков, и карту движения сырья. В частности, инструмент помогает понять, какие расстояния проходит сотрудник, а также заметить, что «вот здесь, например, сотрудник проходит на 300 метров больше, чем надо, а к какой-то операции возвращается два раза, хотя достаточно одного». Рамиль Яруллин считает, что такой подход «позволяет совершенно иначе посмотреть на производство».
Как выяснилось, мешала производству и традиционная для российских компаний проблема захламленности рабочих мест, поэтому сотрудники тратили большое количество времени на поиск инструментов, сырья и материалов. Рабочая группа на выбранном участке применила систему 5С — рациональную организацию рабочего пространства, в основе которой — сортировка вещей, организация хранения и постоянное поддержание порядка. Данному инструменту обучены несколько сотрудников компании, которые стали внутренними тренерами. В свою очередь, они провели обучение работников на предприятии, и система стала внедряться повсеместно. И это не замедлило принести свои плоды: благодаря эффективному инструменту удалось сократить время выполнения операций на 15 процентов, а мусора было вывезено два грузовика.
По словам Рамиля Яруллина, «согласно методологии, мы провели рабочие места в порядок, и сейчас нам уже не нужно давать специальную команду» для того, чтобы поддерживать их в этом качестве постоянно. «Порядок на рабочих местах у нас есть всегда», — с гордостью говорит инженер. «Сотрудники больше не работают в режиме “вечного тушения пожаров”, — продолжает он. — У них появилось время, которое раньше уходило на поиски чего-либо или бессмысленные перемещения». Рамиль Яруллин уверен, что проведенные мероприятия позволили создать благоприятную рабочую среду для сотрудников, в которой им «безопасно и приятно работать».
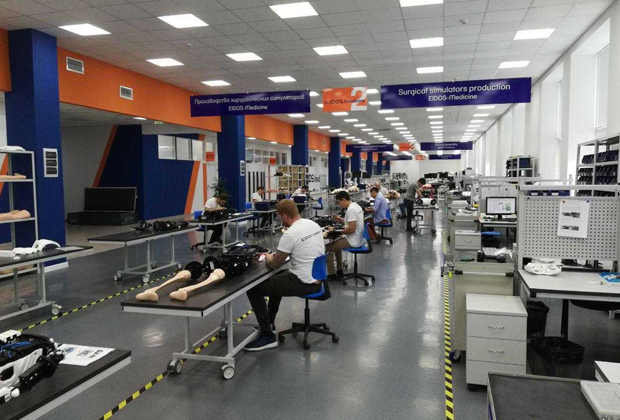
Фото: ФЦК
Надо сказать, что большое количество сотрудников «Эйдос-Медицины» загорелось идеями бережливого производства. Как результат, в компании была внедрена также система «менеджмент подачи идей», позволяющая любому сотруднику обратиться к руководству компании с инициативой по улучшению качества труда. Для этого был разработан специальный бланк подачи такого предложения. Если оно соответствует требованиям, компания его сразу же внедряет, а предложивший получает небольшое денежное вознаграждение — 450 рублей. По словам Рамиля Яруллина, «кому-то это может показаться ерундой, но благодаря постоянному внедрению вот таких небольших улучшений в долгосрочной перспективе мы получаем ощутимый эффект». «Я, например, недавно стажировался на производстве в Германии и там с удивлением узнал, что практически на каждом предприятии менеджмент идей — обычная практика. Мировой опыт показывает, что это дает колоссальные результаты: на Тойоте, например, уже более 40 миллионов предложений», — рассказал представитель «Эйдос-Медицины».
Но главное, по мнению Рамиля Яруллина, это то, что сотрудники оказываются вовлеченными в производственные процессы компании и могут на них влиять. Это позволяет им «не чувствовать себя машиной или болтиком каким-нибудь, выполняющим исключительно монотонную работу», что позитивно сказывается на эффективности работы. За период реализации проекта время протекания процесса снизилось на 94,71 процента. При этом прирост производительности труда по итогам реализации проекта — 22 процента.
Чисто и быстро
Нижегородский масложировой комбинат (НМЖК) — производитель многих известных брендов, крупное предприятие масложировой промышленности, основанное еще в советское время. По словам индустриального директора НМЖК Сергея Бобровского, «в современных конкурентных рыночных условиях повышение внутренней эффективности компании — это жизненная необходимость». Он также отметил, что совместный проект с ФЦК стал одним из первых системных шагов в развитии производственной системы НМЖК.
Эксперты ФЦК в течение первых трех месяцев ежедневно присутствовали на площадке компании в Нижнем Новгороде и принимали участие в работе производства. Здесь так же, как и в «Эйдос-Медицине», было решено начать с пилотного проекта, который был запущен на участке производства соусов «Astoria». Основной проблемой этого сегмента были длительные простои из-за того, что много времени тратилось на мойку линии после смены ассортиментных позиций: почти 12 часов (после оптимизации это время сократилось до 9 часов), это — причина более половины простоев. А у предприятия — очень развитая линейка продуктов.
Сотрудники НМЖК при участии экспертов ФЦК проанализировали процессы производства и внедрили ряд существенных изменений. Например, мойку производственной линии предложили начинать раньше, перераспределили функции по разборке оборудования между сотрудниками, а рядом с линией создали места для хранения инвентаря и средств индивидуальной защиты.
Фото: предоставлено пресс-службой НМЖК
«Общим результатом стало значительное сокращение времени производственных процессов — практически на 3 часа в день», — сообщил Сергей Бобровский. «НМЖК рассчитывает, что загрузка двух линий на это время может принести около 2,4 миллиона рублей дополнительной прибыли в месяц. Сокращение времени техобслуживания и смены рулона могут дать в сумме еще около 0,37 миллиона рублей ежемесячно», — подчеркивает представитель предприятия.
Как следствие, проекты по технологиям бережливого производства были запущены на Урюпинском и Сорочинском маслоэкстракционных заводах, входящих в группу НМЖК. «Следующим шагом станет старт интегрированного проекта “Бережливое производство”, который охватит всю цепочку создания ценности: от поставки сырья и производства до отгрузки клиенту и полки супермаркета, — делится планами Бобровский. — Сейчас мы ставим перед собой амбициозные цели по ликвидации потерь, созданию культуры непрерывного совершенствования и обеспечению высочайшего качества продуктов и услуг».
Зарплата выше
«Белгородские молочные фермы» — часть крупного агрохолдинга «Зеленая долина». И нехарактерный участник нацпроекта. Поясним, почему. Предприятие занимается разведением коров и производством молока. Ольга Тарасова, заместитель директора по повышению эффективности производства, вспоминает, что «когда запускался проект, сельскохозяйственные предприятия не брались, только промышленные. Но нам удалось уговорить ФЦК на эксперимент, и мы стали его участниками». Сегодня отрасль сельского хозяйства — одна из пяти несырьевых отраслей экономики, с которыми работают в рамках нацпроекта. В их числе — обрабатывающие производства, строительство, транспортировка и хранение, ЖКХ.
В феврале 2019 года на ферму впервые приехали два эксперта ФЦК и два сотрудника РЦК. Эксперты прошли стажировку, чтобы лучше понять характер производственных процессов данного сельскохозяйственного предприятия, с тем, чтобы полученный опыт можно было применить для дальнейшего внедрения бережливых технологий и на других сельхозпредприятиях Белгородской области, региона преимущественно аграрного.
На предприятии в качестве пилотного потока был выбран поток производства молока, занимающий 52 процента выручки. Диагностика показала ряд проблем: потери от ожидания операторами машинного доения, как следствие, неравномерная нагрузка работников, лишние перемещения персонала.
Чтобы решить эти проблемы, был разработан стандарт выполнения операций. Это позволило сократить время цикла обслуживания животных в процессе доения с 15:45 до 13:33 минут. Кроме того, были исключены лишние перемещения персонала: теперь запасы расходного материала пополняли вспомогательные работники доильного зала. Также была внедрена та самая система 5С. Как итог: количество производимого молока увеличилось с 50 до 55 тонн в сутки.
Представители экспертной группы также выбрали двух сотрудников из работников предприятия. Они будут внутренними тренерами — это сотрудники, способные ретранслировать полученные знания по всему предприятию и обучить всю остальную команду. Ольга Тарасова вспоминает, что сотрудники ФЦК к ним «приезжали три раза в неделю в течение трех месяцев, потом еще в течение трех месяцев сопровождали удаленно». Тарасова и сейчас твердо уверена, что если позвонит в ФЦК с каким-то вопросом, то ей ответят и обязательно решат ее проблему. «Помощь идет со всех сторон, еще не было случая, чтобы нам не помогли», — подчеркивает она и отмечает при этом, что тоже стала одним из внутренних тренеров. По словам Тарасовой, знаниями, полученными в проекте, она очень довольна и собирается свои компетенции повышать. «Мы знакомимся с успешными проверенными практиками, и это замечательно. Нам дают советы — и это работает», — говорит она.
При этом, по ее словам, до визита экспертов ФЦК процесс дойки на предприятии отлаживал западный специалист с мировым именем. Однако помощь со стороны Федерального центра компетенций во внедрении бережливых технологий позволила ферме еще больше расширить производство. «Мы поставили еще животных, потому что у работников появилось дополнительное время на их дойку, хотя до этого все было впритык, и доить удавалось только два раза в день вместо оптимальных трех раз. Таким образом мы улучшили результат, который этот именитый специалист считал образцовым», — подчеркивает Тарасова.
Кроме того, после оптимизации у доярок появился пятнадцатиминутный перерыв, которого до этого не было. В свою очередь, коровы стали давать больше молока. То есть, по словам Ольги Тарасовой, «экономические показатели увеличились и, одновременно, улучшилось здоровье животных». «Зарплата у нас напрямую зависит от количества молока, а его стало больше. Больше молока — выше зарплата!» — порадовалась она.
Сложный, но результативный
ФЦК завершил работу на 180 предприятиях. Сейчас к нацпроекту присоединись уже более тысячи предприятий. К 2024 году их станет 10 тысяч. Они должны в течение трех лет повысить производительность труда на 30 процентов. Планы амбициозные, но, как уверяет генеральный директор ФЦК Николай Соломон, ресурсный потенциал достаточен для того, чтобы их реализовать: в организации работают более 350 человек, имеющих опыт развития производственных систем в таких компаниях, как Росатом, РЖД, Сбербанк, «Северсталь». В регионах открываются региональные центры компетенций, постоянно идет обучение специалистов предприятий культуре бережливого производства: сейчас обучено более десяти тысяч сотрудников, а через пять лет их должно стать 79,5 тысячи.
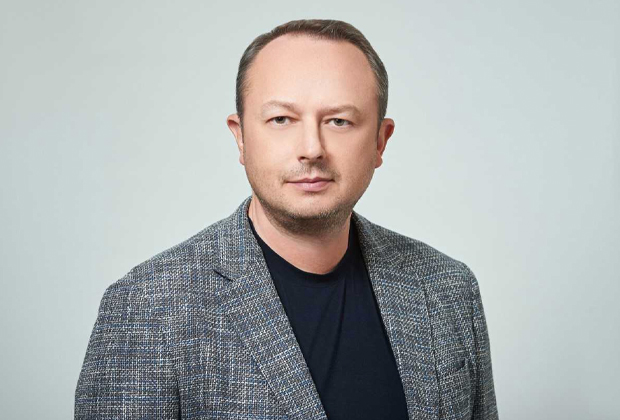
Николай Соломон
Фото: ФЦК
«Основная задача нашего проекта в глобальном смысле — повысить эффективность предприятий настолько, чтобы выйти на стабильный уровень роста производительности труда не менее 5 процентов в год в несырьевых отраслях. Что это значит локально для каждой компании? Сокращение издержек, снижение себестоимости продукции, повышение прибыли, обеспечение спроса рынка. Для отдельного сотрудника — улучшение условий труда, увеличение зарплаты, возможность развития», — подчеркнул Николай Соломон.
Однако помимо экспертности своих сотрудников, во главу угла Николай Соломон ставит общую вовлеченность в процесс, начиная от органов региональной власти (в 2020 году к нацпроекту присоединится вся страна, но уже сейчас подписаны соглашения с 80 регионами) и заканчивая — самое главное — руководителями компаний, которые должны стать действительными лидерами на пути к внедрению на предприятиях культуры непрерывных улучшений.